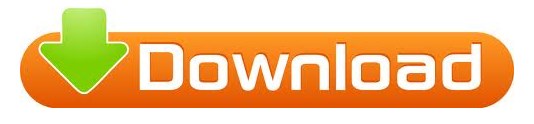
For example, 1% is typically considered a slow mix, 2% is a common supplier specification, and 3% would be a fast curing mix. Thorough mixing is important, and the ratio of catalyst to resin weight affects cure rate and, potentially, the degree of cure.
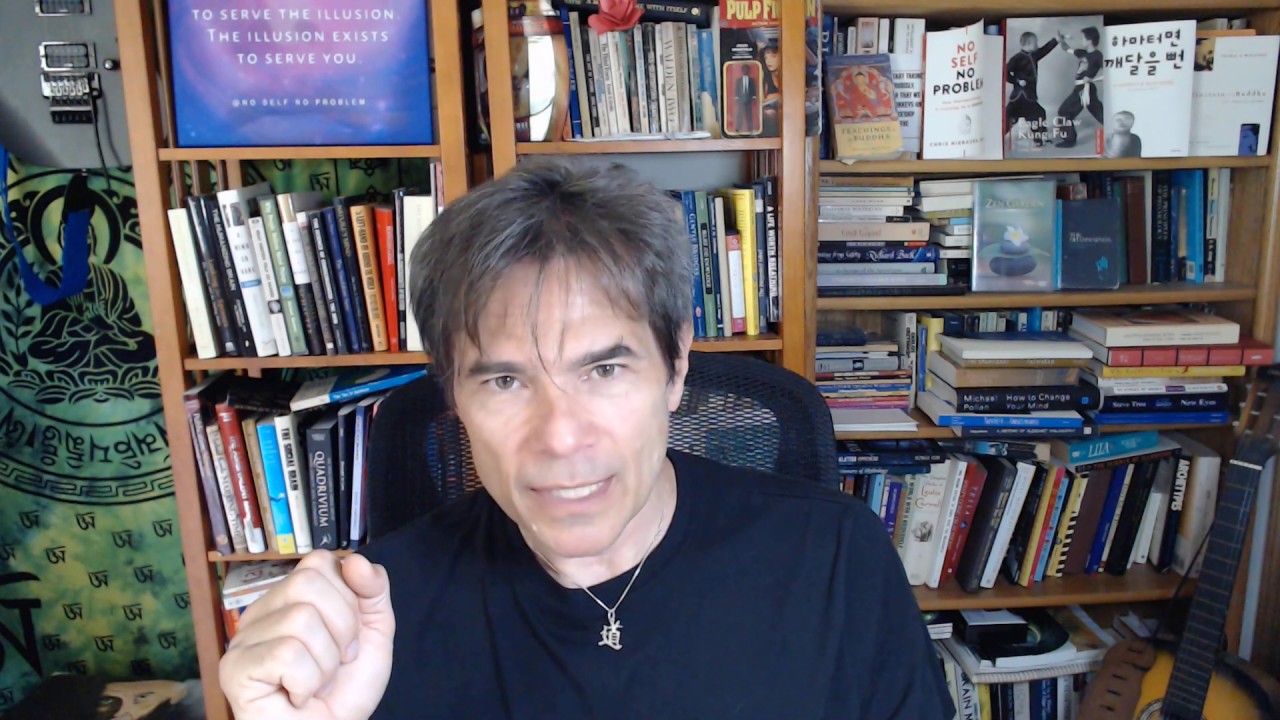
Catalysts used with polyester include Methyl ethyl ketone peroxide (MEKP) and peroxide. Catalysts are added to the resin prior to molding, to activate crosslinking, but do not take part in the polymerization reaction. Even without inhibitors, polyester’s rate of polymerization is too slow to make it practical, as-is, for composite molding, so catalysts and accelerators are added to speed cure. Thus, small amounts of inhibitor are often added during resin manufacture to slow this action and increase the resin’s shelf life. However, polyester resins will gel on their own over a long period of time. Styrene enables polyester resins to cure from a liquid to a solid by crosslinking the molecular chains. However, DCPD solidifies at room temperature and, therefore, requires heated storage and handling facilities. can have lower viscosity and provide good properties at lower styrene content. Dicyclopentadiene (DCPD)-modifed polyesters.
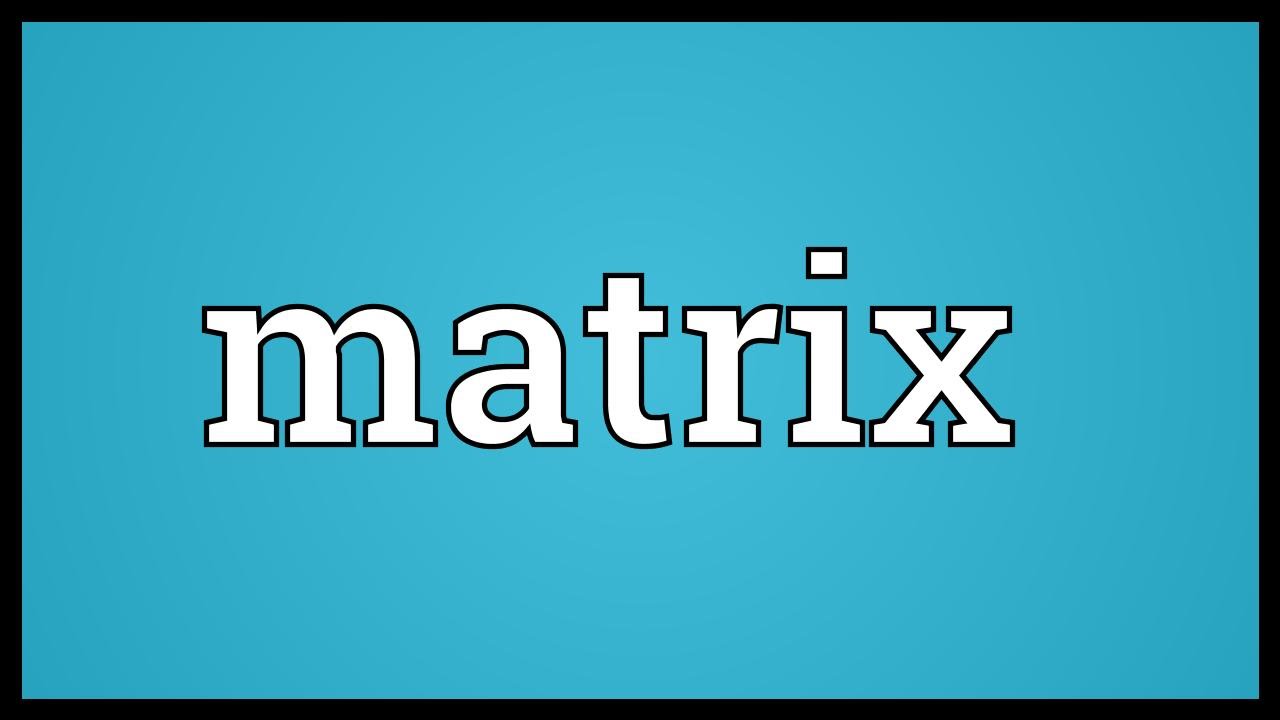
Terephthalic polyester resins incorporate terephthalic acids and have been formulated for improved toughness, compared to conventional isopolyesters. Isopolyester resins have isophthalic acid as their essential ingredient and exhibit superior chemical and thermal resistance, compared to orthopolyesters. Orthopolyesters, for example, build on orthophthalic acid. Polyester resins are often differentiated in terms of their base ingredients. Styrene is added in amounts up to 50% to reduce viscosity, making the resin easier to handle and process. The properties of polyester formulations can be modified to meet specific performance criteria, based on the selection of glycol and acid elements and reactive monomers (most commonly, styrene). Polyesters provide the primary resin matrix used in bulk molding compounds (BMC) and sheet molding compounds (SMC), which are processed using compression molding (see "Fabrication methods,").

(Saturated polyesters are thermoplastic polymers.) Typically coupled with glass fiber reinforcements, polyesters adapt well to a range of fabrication processes and are most commonly used in open-mold sprayup, compression molding, resin transfer molding (RTM) and casting. Unsaturated polyester resins are the most widely used thermosets in commercial, mass-production applications, thanks to their ease of handling, good balance of mechanical, electrical and chemical properties, and relatively low cost. Leveraging motorsports composites for next-gen rotorcraft Developed primarily in an effort to use renewable agricultural feedstocks, bio-resins comprise, in varying proportions, polyol (from soybeans) and ethanol (from corn). Although almost all thermosets in commercial use today are derived from petroleum feedstocks, R&D and commercialization is ongoing in the growing field of bio-resins. After cure, a thermoset cannot be returned to its uncured state. The polymers most widely used in composites are thermosets, a class of plastic resins that, when cured by thermal and/or chemical (catalyst or promoter) or other means, become substantially infusible and insoluble.
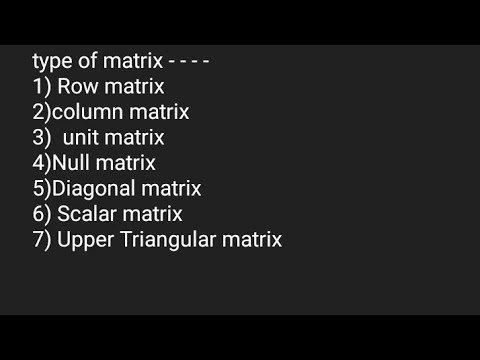
Carbon as a matrix is used in extreme high-temperature applications, such as carbon/carbon brakes and rocket nozzles. Ceramic and metal matrices are typically used in very high-temperature environments, such as engines. Polymer matrices are the most widely used for composites in commercial and high-performance aerospace applications. A composite matrix may be a polymer, ceramic, metal or carbon. The matrix binds the fiber reinforcement, transfers loads between fibers, gives the composite component its net shape and determines its surface quality.
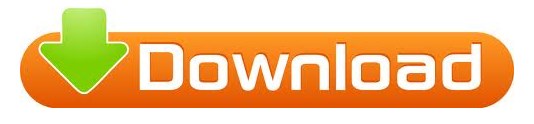